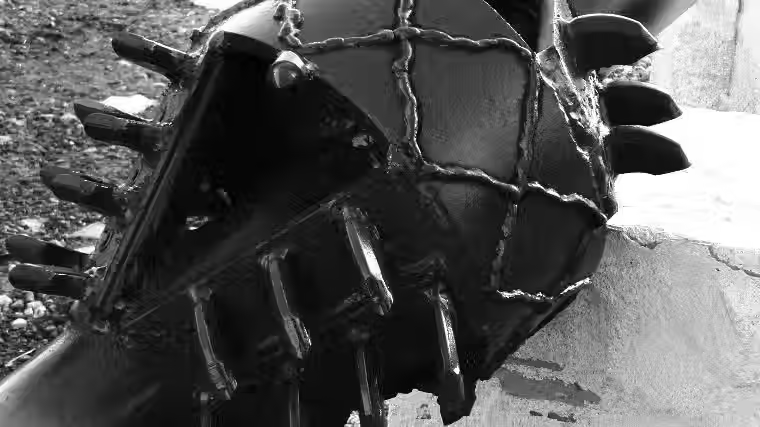
A well-maintained barrel reamer can precisely cut up to 100 firearm chambers without requiring resharpening, making it one of the most crucial tools in precision gunsmithing. Chamber reamers, specifically designed for cutting the chambers of handguns, rifles, and shotguns, operate with exacting precision at speeds between 200 to 300 RPM.
These specialized cutting tools, typically crafted from high-speed steel, come in two main types: solid pilot reamers and floating pilot reamers. While solid pilot reamers offer greater durability and cost-effectiveness, floating pilot reamers provide self-centering capabilities essential for accommodating barrel variations. Most manufacturers produce these reamers to SAAMI specifications, ensuring proper headspace and compatibility with factory ammunition.
This comprehensive guide explores the critical factors in selecting the right reamer for precision machining, including material considerations, technical specifications, and maintenance requirements that directly impact firearm accuracy and performance.
Understanding Different Types of Barrel Reamers
"A barrel reamer is a type of horizontal directional drilling (HDD) tool used to enlarge the diameter of a borehole. It has a relatively flat face lined with rows of carbide cutters that allow the reamer to cut and open the hole slightly larger than the diameter of its solid body." — StraightLine HDD, Leading manufacturer of horizontal directional drilling equipment
Barrel reamers represent precision cutting tools capable of achieving tolerances as tight as 0.0002 inches, making them essential for firearms that demand perfect chamber dimensions. These specialized tools come in several distinct configurations, each designed for specific applications in the barrel chambering process.
Solid Pilot vs. Floating Pilot Chamber Reamers
The choice between solid and floating pilot chamber reamers significantly impacts both precision and versatility. Solid pilot reamers feature a fixed-size pilot ground directly into the tool, ensuring perfect concentricity between the pilot and cutting surfaces. These reamers typically cost less than their floating counterparts since they require less manufacturing complexity.
In contrast, floating (removable) pilot reamers utilize interchangeable hardened bushings that can be swapped to match specific barrel dimensions. This design allows gunsmiths to select a pilot that provides exactly the desired clearance with a particular bore. For optimal results, these bushings should be only 0.0002-0.0004 inches smaller than the barrel bore diameter.
The industry has seen a notable shift in preference over time. According to manufacturing observations, the ratio has changed from five solid pilot reamers sold for every removable pilot reamer to approximately one-to-one today. This evolution reflects increasing demands for customization and precision in modern gunsmithing.
Roughing, Finishing, and Specialty Reamers
Production environments typically employ both roughing and finishing reamers for optimal results. Roughing reamers perform the initial heavy cutting, removing bulk material but stopping short of final dimensions. These tools generally feature fewer flutes to facilitate better chip evacuation during the high-volume material removal process.
Finishing reamers subsequently create the final chamber dimensions, ensuring smooth surfaces and precise tolerances. Unlike roughers, finishing reamers include features specifically designed to cut the freebore and throat areas—the critical transition zone between the chamber and rifling. The throat should ideally be angled at approximately two degrees for optimal performance.
Although some gunsmiths report success using only finishing reamers for complete chambering operations, others maintain that utilizing both types extends tool life and produces superior results. When chambering a barrel, many professionals use a floating reamer holder mounted in the tailstock of a lathe to prevent damage to the rifling.
Single-Flute vs. Multi-Flute Designs
The number and configuration of flutes directly influence a reamer's performance characteristics. Multi-blade designs with unequally spaced cutting edges provide advantages in precision, cutting speed, and surface quality. These asymmetrical patterns help reduce vibration and chatter during operation.
Chamber reamers feature either straight or helical flute patterns. Although straight flutes cost less to manufacture, helical designs excel at eliminating linear chatter marks. Additionally, reamers with an odd number of flutes help mitigate vibration and harmonics during cutting operations, though this makes manufacturing and measurement more challenging.
For precision machining applications, pressure lubrication systems similar to those used by gunsmiths prove valuable. These systems continuously flush chips backward while providing lubrication, minimizing built-up edge formation and improving surface finish quality.
Each reamer configuration presents distinct advantages for specific applications, requiring gunsmiths to select the appropriate type based on the particular chambering requirements, desired precision level, and production volume.
Materials and Construction Quality Factors
Selecting the optimal material for barrel reamers hinges on several critical factors that directly impact performance, tool life, and machining precision. The material choice proves particularly crucial for gunsmiths seeking precise chamber dimensions in their custom firearms projects.
High-Speed Steel (HSS) vs. Carbide Options
High-speed steel represents the traditional choice for chamber reamers, offering excellent versatility and cost-effectiveness. HSS tools provide distinct advantages for individual gunsmiths and low-to-medium volume manufacturers, primarily due to their forgiving nature with less-than-optimal feeds and speeds. Furthermore, HSS reamers resist shattering when accidentally dropped, unlike their carbide counterparts.
Carbide reamers, conversely, outperform HSS in several key metrics. These tools last significantly longer than high-speed steel versions and can operate at higher spindle speeds with faster cycle times. For production environments, carbide chamber reamers offer compelling benefits despite their higher initial cost. However, they require more rigid machinery and precisely controlled feed rates to function optimally.
One notable consideration: carbide proves especially valuable when working with harder-than-average barrels, such as chrome-washed or those exceeding 40 Rockwell hardness. Nevertheless, their brittleness makes them susceptible to chipping, requiring careful handling and storage.
Coating Technologies for Extended Reamer Life
Modern coating technologies dramatically enhance reamer performance and longevity. Titanium CarboNitride (TiCN) coating infuses a microscopic layer (0.0001"-0.0002") into the surface of HSS reamers. This extremely hard, "slippery" coating delivers superior surface finishes and at least doubles the tool life of uncoated HSS.
The economics of coated reamers merit consideration. At approximately $18 per coating application, doubling the life of a $100 reamer represents an excellent value proposition. This proves particularly advantageous for gunsmiths who regularly chamber popular cartridges like the .308 Winchester.
Though Titanium Nitride (TiN) "gold" coating has been used historically, it generally proves less effective for cutting tools than TiCN. TiCN appears light-to-dark gray, sometimes with a distinctive pink tint.
Evaluating Flute Geometry and Cutting Edges
The configuration of flutes and cutting edges profoundly influences reamer performance. Four-flute designs commonly appear in rougher reamers, while six-flute configurations typically characterize finishing reamers. Five-flute options have gained popularity, particularly for 5R rifling applications.
Regarding flute design, both straight and spiral options exist. Straight flutes represent the traditional, most common approach. Spiral flutes theoretically deliver better finishes with reduced chatter, though practical differences often prove minimal.
The cutting edge geometry demands careful examination. Finish reamers feature cutting edges nearly 90 degrees to the centerline, creating flat surfaces ideal for breaking chips into small pieces. Behind this edge, two relief grinds—primary (margin) and secondary—facilitate smooth cutting. The primary relief presents a shallow angle, while the secondary relief angles more steeply to prevent chip clogging.
Importantly, flutes are typically designed with slight asymmetry, featuring intentionally varied dimensions. Rather than representing manufacturing defects, these variations strategically reduce harmonics and chatter during operation. This seemingly minor detail significantly enhances the reamer's overall cutting performance.
Matching Reamers to Your Specific Firearm Project
"Are you chasing that new cartridge or wildcat? Do you have an idea for a new cartridge and need a reamer to match your vision? You've come to the right place." — JGS Precision, Manufacturer of precision reamers and gages
Choosing the precise chamber reamer represents a critical decision for any custom firearm project. Whether working with factory cartridges or custom wildcats, the selection process directly influences accuracy, ammunition compatibility, and overall performance.
Standard SAAMI vs. Custom Chamber Specifications
Sporting Arms and Ammunition Manufacturers' Institute (SAAMI) specifications provide standardized dimensions that ensure factory ammunition functions reliably across different firearms. Consequently, many gunsmiths utilize SAAMI-spec reamers for their builds. These standardized reamers create chambers with appropriate headspace and dimensions to accommodate commercial ammunition.
Custom chamber specifications, meanwhile, offer notable advantages over standard SAAMI dimensions. Tighter chambers extend case lifespan by reducing material movement during firing and reloading. Custom chambers also improve concentricity, enhancing accuracy potential for precision applications. For competitive disciplines like F-Class, custom chamber specifications often deliver superior performance.
Custom specifications typically focus on optimizing:
Neck diameter (usually tighter than SAAMI)
Body dimensions (with precise clearances)
Shoulder angle and position
Throat geometry
Considerations for Different Calibers and Cartridges
When selecting a barrel reamer for a specific caliber, matching it to your intended ammunition proves essential. For hunting rifles, a chamber reamer that accommodates various bullet weights offers versatility. Essentially, a chamber designed for 180-grain bullets may not function optimally with 210-grain projectiles.
Some gunsmiths recommend taking the actual ammunition you plan to shoot and having a reamer made specifically for those dimensions. This approach ensures perfect compatibility between your chamber and preferred loads. For precision applications, this harmony between chamber and ammunition delivers superior accuracy.
Throat length and freebore diameter merit careful consideration during reamer selection. The throat should accommodate your preferred bullet seating depth while maintaining sufficient case neck engagement. For optimal performance, some experts recommend specifying freebore diameter at 0.0003 inches over the maximum diameter of your largest bullet.
Wildcatting and Custom Chambering Requirements
Wildcat cartridges—modified versions of factory cartridges—require specialized reamers tailored to their unique dimensions. Popular modifications include Ackley Improvements (featuring sharper shoulder angles), caliber changes through necking up or down, and custom throat configurations.
For wildcatting projects, several approaches exist for obtaining appropriate reamers:
Send dummy rounds loaded with your preferred bullet to the reamer manufacturer
Provide detailed specifications including body dimensions, neck diameter, and throat configuration
Send fired cases from your dies to ensure perfect compatibility
Custom reamer costs typically add $200-300 to a build, yet provide invaluable precision for serious shooters. Ultimately, this investment proves worthwhile for achieving optimal accuracy and performance from custom chamberings.
Regardless of your specific project, matching your reamer precisely to your intended application ensures optimal results and maximizes the potential of your custom firearm.
Technical Specifications That Impact Performance
Precise technical specifications serve as the foundation for optimal barrel reamer performance. Beyond reamer selection, operational parameters directly influence chamber quality, tool life, and accuracy of the final product.
Optimal Cutting Speeds for Different Materials
The optimal cutting speed for chamber reamers varies significantly among gunsmiths. Some manufacturers recommend faster speeds between 150-300 RPM with aggressive feed rates. Yet, experienced gunsmiths often prefer much slower speeds around 60-70 RPM. This discrepancy reflects how different approaches work in various applications.
For heat-treated metals or military-specification 4140 steel barrels, petroleum-based cutting oils with high sulfur content often yield superior results. Specific recommended cutting fluids include:
TRIM OM 300
Castrol ILOCUT 534
Texaco Transultex H
Feed Rate Calculations for Precision Results
Feed rates critically impact chamber finish quality. Firstly, start with the manufacturer's recommended low-range surface feet per minute (SFM), then gradually increase feed rate in small increments of 0.001-0.0015 per revolution until reaching optimal performance. Subsequently, increase speed in 10-20 SFM increments until undesirable conditions appear.
Fred Zeglin, a respected gunsmith, notes that slower speeds effectively reduce chatter—a common issue that typically appears when the reamer's shoulder engages the workpiece. Moreover, if chatter occurs, several effective solutions exist:
Using a slot-cut patch over the shoulder area with cutting oil
Wrapping wax paper in a spiral around the reamer
Applying beeswax or heavy gear grease to the reamer
Tolerance Considerations in Precision Machining
Chamber reamers typically deliver tolerances within +/- 0.0002 inches when properly operated. Optimal results require the bushing-to-bore fit tolerance no greater than -0.0005 inches. Additionally, tightening the reamer holder to approximately 0.002 inches more float than the maximum allowable bore runout ensures proper alignment.
The final chamber should exhibit a surface finish between 6-16 RMS (Root Mean Square), completely free of chatter marks or scratches. Indeed, poor surface finish often indicates either contaminated cutting fluid or improper cutting parameters rather than tool deficiencies.
Maintenance and Care of Precision Barrel Reamers
Extended service life for chamber reamers depends primarily on implementing consistent maintenance practices. Without proper care, even premium reamers quickly lose their cutting effectiveness, potentially damaging expensive firearms projects.
Proper Cleaning Techniques Between Operations
Regular inspection and cleaning prevent performance-degrading build-up on chamber reamers. After each use, examine cutting edges carefully for aluminum build-up—a common issue that accumulates gradually yet significantly impacts cutting ability. For detailed inspection, utilize an eye loupe or run a penny along the edges to detect irregularities.
For effective cleaning:
Apply a fine-grit diamond honing tool (such as EZ-LAP-HONE) to remove build-up
Draw the tool forward smoothly along each cutting edge 3-4 times
Inspect between passes to avoid excessive material removal
Clean each cutting edge thoroughly until all residue disappears
Between reaming operations, always remove drilling mud and debris completely. This step becomes exceptionally important when working with precision chambers.
Sharpening Procedures and When to Resharpen
Professional gunsmiths typically inspect reamers after every use and normally retire them after 15-20 barrels—especially with high-quality 416 stainless steel barrels. Sharpening becomes necessary when requiring excessive force or producing inconsistent results.
Initially, reamers made to minimal dimensions offer limited resharpening potential, whereas those manufactured to larger specifications provide additional material for honing. Sending reamers for professional resharpening often includes a "set-back" procedure that removes material behind the cutting edges.
Storage Solutions to Prevent Damage
Proper storage extends reamer life substantially. Dedicated plastic storage tubes protect precision edges from accidental damage. These purpose-built containers secure reamers against environmental threats, including humidity, temperature fluctuations, and exposure to corrosive elements.
After cleaning, ensure reamers are completely dry before storage. Many professionals apply light oil coatings—specifically G96 oil receives recommendations from experienced gunsmiths. For optimal protection, use storage racks or containers that prevent contact between cutting edges and other tools.
Conclusion
Barrel reamers stand as essential tools for achieving precision in firearm chambering operations. Through careful consideration of reamer types, materials, and specifications, gunsmiths can consistently produce chambers that meet exacting tolerances down to 0.0002 inches.
Successful chamber reaming operations depend on several key factors. First, selecting between solid and floating pilot designs based on specific application requirements. Second, matching material choices like HSS or carbide to production volumes and operating conditions. Third, maintaining proper cutting speeds and feed rates while adhering to recommended maintenance protocols.
Professional gunsmiths achieve optimal results by following manufacturer-specified parameters, using appropriate cutting fluids, and implementing regular inspection routines. These practices, combined with proper storage solutions and timely resharpening, ensure maximum tool life and consistent chamber quality.
The field of precision gunsmithing continues advancing with improved coating technologies and specialized designs for custom applications. Whether working on standard SAAMI chambers or developing custom wildcats, understanding these fundamental aspects helps craftsmen deliver firearms that meet increasingly demanding accuracy requirements.
FAQs
Q1. What factors should I consider when choosing a barrel reamer? When selecting a barrel reamer, consider the type (solid pilot vs. floating pilot), material (HSS vs. carbide), flute design, and whether you need a roughing or finishing reamer. Also, match the reamer to your specific firearm project, considering standard SAAMI or custom chamber specifications.
Q2. How do cutting speeds affect barrel reamer performance? Cutting speeds significantly impact reamer performance. While some manufacturers recommend speeds between 150-300 RPM, experienced gunsmiths often prefer slower speeds around 60-70 RPM. The optimal speed depends on the material being cut and the desired finish quality.
Q3. What maintenance practices extend the life of a barrel reamer? Regular cleaning after each use, proper storage in dedicated containers, and applying a light oil coating can extend reamer life. Inspect cutting edges for build-up, use diamond honing tools for cleaning, and consider professional resharpening when performance declines.
Q4. How often should barrel reamers be replaced or resharpened? Professional gunsmiths typically inspect reamers after every use and often retire them after 15-20 barrels, especially when working with high-quality stainless steel. Resharpening becomes necessary when the reamer requires excessive force or produces inconsistent results.
Q5. What are the advantages of custom chamber specifications over SAAMI standards? Custom chamber specifications can offer tighter tolerances, extended case life, improved concentricity, and enhanced accuracy potential. They allow for optimization of neck diameter, body dimensions, shoulder angle, and throat geometry to match specific ammunition and shooting requirements.
Show facts
Comments